A few nice surface grinding aluminum images I found:
Steven F. Udvar-Hazy Center: main hall panorama (F-4 Corsair, et al)
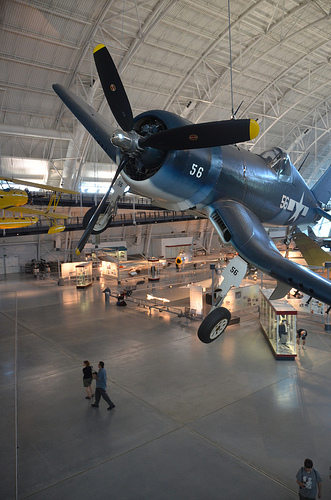
Image by Chris Devers
See more photos of this, and the Wikipedia article.
Details, quoting from Smithsonian National Air and Space Museum | Vought F4U-1D Corsair:
By V-J Day, September 2, 1945, Corsair pilots had amassed an 11:1 kill ratio against enemy aircraft. The aircraft’s distinctive inverted gull-wing design allowed ground clearance for the huge, three-bladed Hamilton Standard Hydromatic propeller, which spanned more than 4 meters (13 feet). The Pratt and Whitney R-2800 radial engine and Hydromatic propeller was the largest and one of the most powerful engine-propeller combinations ever flown on a fighter aircraft.
Charles Lindbergh flew bombing missions in a Corsair with Marine Air Group 31 against Japanese strongholds in the Pacific in 1944. This airplane is painted in the colors and markings of the Corsair Sun Setter, a Marine close-support fighter assigned to the USS Essex in July 1944.
Transferred from the United States Navy.
Manufacturer:
Vought Aircraft Company
Date:
1940
Country of Origin:
United States of America
Dimensions:
Overall: 460 x 1020cm, 4037kg, 1250cm (15ft 1 1/8in. x 33ft 5 9/16in., 8900lb., 41ft 1/8in.)
Materials:
All metal with fabric-covered wings behind the main spar.
Physical Description:
R-2800 radial air-cooled engine with 1,850 horsepower, turned a three-blade Hamilton Standard Hydromatic propeller with solid aluminum blades spanning 13 feet 1 inch; wing bent gull-shaped on both sides of the fuselage.
Long Description:
On February 1, 1938, the United States Navy Bureau of Aeronautics requested proposals from American aircraft manufacturers for a new carrier-based fighter airplane. During April, the Vought Aircraft Corporation responded with two designs and one of them, powered by a Pratt & Whitney R-2800 engine, won the competition in June. Less than a year later, Vought test pilot Lyman A. Bullard, Jr., first flew the Vought XF4U-1 prototype on May 29, 1940. At that time, the largest engine driving the biggest propeller ever flown on a fighter aircraft propelled Bullard on this test flight. The R-2800 radial air-cooled engine developed 1,850 horsepower and it turned a three-blade Hamilton Standard Hydromatic propeller with solid aluminum blades spanning 13 feet 1 inch.
The airplane Bullard flew also had another striking feature, a wing bent gull-shaped on both sides of the fuselage. This arrangement gave additional ground clearance for the propeller and reduced drag at the wing-to-fuselage joint. Ironically for a 644-kph (400 mph) airplane, Vought covered the wing with fabric behind the main spar, a practice the company also followed on the OS2U Kingfisher (see NASM collection).
When naval air strategists had crafted the requirements for the new fighter, the need for speed had overridden all other performance goals. With this in mind, the Bureau of Aeronautics selected the most powerful air-cooled engine available, the R-2800. Vought assembled a team, lead by chief designer Rex Biesel, to design the best airframe around this powerful engine. The group included project engineer Frank Albright, aerodynamics engineer Paul Baker, and propulsion engineer James Shoemaker. Biesel and his team succeeded in building a very fast fighter but when they redesigned the prototype for production, they were forced to make an unfortunate compromise.
The Navy requested heavier armament for production Corsairs and Biesel redesigned each outboard folding wing panel to carry three .50 caliber machine guns. These guns displaced fuel tanks installed in each wing leading edge. To replace this lost capacity, an 897-liter (237 gal) fuselage tank was installed between the cockpit and the engine. To maintain the speedy and narrow fuselage profile, Biesel could not stack the cockpit on top of the tank, so he moved it nearly three feet aft. Now the wing completely blocked the pilot’s line of sight during the most critical stages of landing. The early Corsair also had a vicious stall, powerful torque and propeller effects at slow speed, a short tail wheel strut, main gear struts that often bounced the airplane at touchdown, and cowl flap actuators that leaked oil onto the windshield. These difficulties, combined with the lack of cockpit visibility, made the airplane nearly impossible to land on the tiny deck of an aircraft carrier. Navy pilots soon nicknamed the F4U the ‘ensign eliminator’ for its tendency to kill these inexperienced aviators. The Navy refused to clear the F4U for carrier operations until late in 1944, more than seven years after the project started.
This flaw did not deter the Navy from accepting Corsairs because Navy and Marine pilots sorely needed an improved fighter to replace the Grumman F4F Wildcat (see NASM collection). By New Year’s Eve, 1942, the service owned 178 F4U-1 airplanes. Early in 1943, the Navy decided to divert all Corsairs to land-based United States Marine Corps squadrons and fill Navy carrier-based units with the Grumman F6F Hellcat (see NASM collection). At its best speed of 612 kph (380 mph) at 6,992 m (23,000 ft), the Hellcat was about 24 kph (15 mph) slower than the Corsair but it was a joy to fly aboard the carrier. The F6F filled in splendidly until improvements to the F4U qualified it for carrier operations. Meanwhile, the Marines on Guadalcanal took their Corsairs into combat and engaged the enemy for the first time on February 14, 1943, six months before Hellcat pilots on that battle-scared island first encountered enemy aircraft.
The F4U had an immediate impact on the Pacific air war. Pilots could use the Corsair’s speed and firepower to engage the more maneuverable Japanese airplanes only when the advantage favored the Americans. Unprotected by armor or self-sealing fuel tanks, no Japanese fighter or bomber could withstand for more than a few seconds the concentrated volley from the six .50 caliber machine guns carried by a Corsair. Major Gregory "Pappy" Boyington assumed command of Marine Corsair squadron VMF-214, nicknamed the ‘Black Sheep’ squadron, on September 7, 1943. During less than 5 months of action, Boyington received credit for downing 28 enemy aircraft. Enemy aircraft shot him down on January 3, 1944, but he survived the war in a Japanese prison camp.
In May and June 1944, Charles A. Lindbergh flew Corsair missions with Marine pilots at Green Island and Emirau. On September 3, 1944, Lindbergh demonstrated the F4U’s bomb hauling capacity by flying a Corsair from Marine Air Group 31 carrying three bombs each weighing 450 kg (1,000 lb). He dropped this load on enemy positions at Wotje Atoll. On the September 8, Lindbergh dropped the first 900-kg (2,000 lb) bomb during an attack on the atoll. For the finale five days later, the Atlantic flyer delivered a 900-kg (2,000 lb) bomb and two 450-kg (1,000 lb) bombs. Lindbergh went ahead and flew these missions after the commander of MAG-31 informed him that if he was forced down and captured, the Japanese would almost certainly execute him.
As of V-J Day, September 2, 1945, the Navy credited Corsair pilots with destroying 2,140 enemy aircraft in aerial combat. The Navy and Marines lost 189 F4Us in combat and 1,435 Corsairs in non-combat accidents. Beginning on February 13, 1942, Marine and Navy pilots flew 64,051 operational sorties, 54,470 from runways and 9,581 from carrier decks. During the war, the British Royal Navy accepted 2,012 Corsairs and the Royal New Zealand Air Force accepted 364. The demand was so great that the Goodyear Aircraft Corporation and the Brewster Aeronautical Corporation also produced the F4U.
Corsairs returned to Navy carrier decks and Marine airfields during the Korean War. On September 10, 1952, Captain Jesse Folmar of Marine Fighter Squadron VMF-312 destroyed a MiG-15 in aerial combat over the west coast of Korea. However, F4U pilots did not have many air-to-air encounters over Korea. Their primary mission was to support Allied ground units along the battlefront.
After the World War II, civilian pilots adapted the speedy bent-wing bird from Vought to fly in competitive air races. They preferred modified versions of the F2G-1 and -2 originally built by Goodyear. Corsairs won the prestigious Thompson Trophy twice. In 1952, Vought manufactured 94 F4U-7s for the French Navy, and these aircraft saw action over Indochina but this order marked the end of Corsair production. In production longer than any other U.S. fighter to see service in World War II, Vought, Goodyear, and Brewster built a total of 12,582 F4Us.
The United States Navy donated an F4U-1D to the National Air and Space Museum in September 1960. Vought delivered this Corsair, Bureau of Aeronautics serial number 50375, to the Navy on April 26, 1944. By October, pilots of VF-10 were flying it but in November, the airplane was transferred to VF-89 at Naval Air Station Atlantic City. It remained there as the squadron moved to NAS Oceana and NAS Norfolk. During February 1945, the Navy withdrew the airplane from active service and transferred it to a pool of surplus aircraft stored at Quantico, Virginia. In 1980, NASM craftsmen restored the F4U-1D in the colors and markings of a Corsair named "Sun Setter," a fighter assigned to Marine Fighter Squadron VMF-114 when that unit served aboard the "USS Essex" in July 1944.
• • •
Quoting from Wikipedia | Vought F4U Corsair:
The Chance Vought F4U Corsair was a carrier-capable fighter aircraft that saw service primarily in World War II and the Korean War. Demand for the aircraft soon overwhelmed Vought’s manufacturing capability, resulting in production by Goodyear and Brewster: Goodyear-built Corsairs were designated FG and Brewster-built aircraft F3A. From the first prototype delivery to the U.S. Navy in 1940, to final delivery in 1953 to the French, 12,571 F4U Corsairs were manufactured by Vought, in 16 separate models, in the longest production run of any piston-engined fighter in U.S. history (1942–1953).
The Corsair served in the U.S. Navy, U.S. Marines, Fleet Air Arm and the Royal New Zealand Air Force, as well as the French Navy Aeronavale and other, smaller, air forces until the 1960s. It quickly became the most capable carrier-based fighter-bomber of World War II. Some Japanese pilots regarded it as the most formidable American fighter of World War II, and the U.S. Navy counted an 11:1 kill ratio with the F4U Corsair.
F4U-1D (Corsair Mk IV): Built in parallel with the F4U-1C, but was introduced in April 1944. It had the new -8W water-injection engine. This change gave the aircraft up to 250 hp (190 kW) more power, which, in turn, increased performance. Speed, for example, was boosted from 417 miles per hour (671 km/h) to 425 miles per hour (684 km/h). Because of the U.S. Navy’s need for fighter-bombers, it had a payload of rockets double the -1A’s, as well as twin-rack plumbing for an additional belly drop tank. Such modifications necessitated the need for rocket tabs (attached to fully metal-plated underwing surfaces) and bomb pylons to be bolted on the fighter, however, causing extra drag. Additionally, the role of fighter-bombing was a new task for the Corsair and the wing fuel cells proved too vulnerable and were removed.[] The extra fuel carried by the two drop tanks would still allow the aircraft to fly relatively long missions despite the heavy, un-aerodynamic load. The regular armament of six machine guns were implemented as well. The canopies of most -1Ds had their struts removed along with their metal caps, which were used — at one point — as a measure to prevent the canopies’ glass from cracking as they moved along the fuselage spines of the fighters.[] Also, the clear-view style "Malcolm Hood" canopy used initially on Supermarine Spitfire and P-51C Mustang aircraft was adopted as standard equipment for the -1D model, and all later F4U production aircraft. Additional production was carried out by Goodyear (FG-1D) and Brewster (F3A-1D). In Fleet Air Arm service, the latter was known as the Corsair III, and both had their wingtips clipped by 8" per wing to allow storage in the lower hangars of British carriers.
Steven F. Udvar-Hazy Center: Air France Concorde
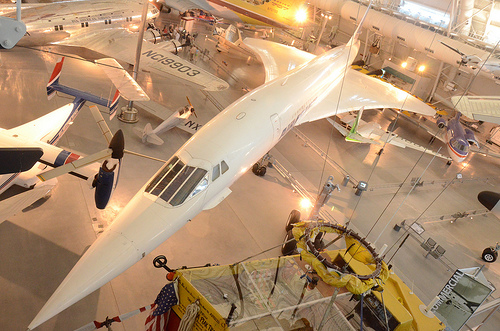
Image by Chris Devers
Quoting Smithsonian National Air and Space Museum | Concorde, Fox Alpha, Air France:
The first supersonic airliner to enter service, the Concorde flew thousands of passengers across the Atlantic at twice the speed of sound for over 25 years. Designed and built by Aérospatiale of France and the British Aviation Corporation, the graceful Concorde was a stunning technological achievement that could not overcome serious economic problems.
In 1976 Air France and British Airways jointly inaugurated Concorde service to destinations around the globe. Carrying up to 100 passengers in great comfort, the Concorde catered to first class passengers for whom speed was critical. It could cross the Atlantic in fewer than four hours – half the time of a conventional jet airliner. However its high operating costs resulted in very high fares that limited the number of passengers who could afford to fly it. These problems and a shrinking market eventually forced the reduction of service until all Concordes were retired in 2003.
In 1989, Air France signed a letter of agreement to donate a Concorde to the National Air and Space Museum upon the aircraft’s retirement. On June 12, 2003, Air France honored that agreement, donating Concorde F-BVFA to the Museum upon the completion of its last flight. This aircraft was the first Air France Concorde to open service to Rio de Janeiro, Washington, D.C., and New York and had flown 17,824 hours.
Gift of Air France.
Manufacturer:
Societe Nationale Industrielle Aerospatiale
British Aircraft Corporation
Dimensions:
Wingspan: 25.56 m (83 ft 10 in)
Length: 61.66 m (202 ft 3 in)
Height: 11.3 m (37 ft 1 in)
Weight, empty: 79,265 kg (174,750 lb)
Weight, gross: 181,435 kg (400,000 lb)
Top speed: 2,179 km/h (1350 mph)
Engine: Four Rolls-Royce/SNECMA Olympus 593 Mk 602, 17,259 kg (38,050 lb) thrust each
Manufacturer: Société Nationale Industrielle Aérospatiale, Paris, France, and British Aircraft Corporation, London, United Kingdom
Physical Description:
Aircaft Serial Number: 205. Including four (4) engines, bearing respectively the serial number: CBE066, CBE062, CBE086 and CBE085.
Also included, aircraft plaque: "AIR FRANCE Lorsque viendra le jour d’exposer Concorde dans un musee, la Smithsonian Institution a dores et deja choisi, pour le Musee de l’Air et de l’Espace de Washington, un appariel portant le couleurs d’Air France."
Steven F. Udvar-Hazy Center: SR-71 Blackbird top view panorama
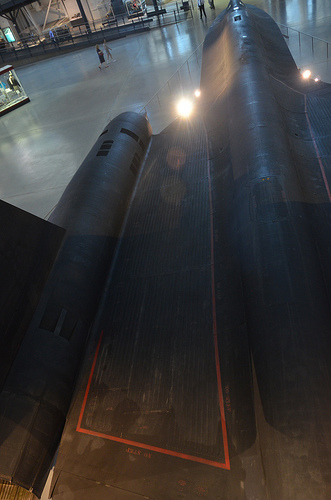
Image by Chris Devers
See more photos of this, and the Wikipedia article.
Details, quoting from Smithsonian National Air and Space Museum | Lockheed SR-71 Blackbird:
No reconnaissance aircraft in history has operated globally in more hostile airspace or with such complete impunity than the SR-71, the world’s fastest jet-propelled aircraft. The Blackbird’s performance and operational achievements placed it at the pinnacle of aviation technology developments during the Cold War.
This Blackbird accrued about 2,800 hours of flight time during 24 years of active service with the U.S. Air Force. On its last flight, March 6, 1990, Lt. Col. Ed Yielding and Lt. Col. Joseph Vida set a speed record by flying from Los Angeles to Washington, D.C., in 1 hour, 4 minutes, and 20 seconds, averaging 3,418 kilometers (2,124 miles) per hour. At the flight’s conclusion, they landed at Washington-Dulles International Airport and turned the airplane over to the Smithsonian.
Transferred from the United States Air Force.
Manufacturer:
Lockheed Aircraft Corporation
Designer:
Clarence L. "Kelly" Johnson
Date:
1964
Country of Origin:
United States of America
Dimensions:
Overall: 18ft 5 15/16in. x 55ft 7in. x 107ft 5in., 169998.5lb. (5.638m x 16.942m x 32.741m, 77110.8kg)
Other: 18ft 5 15/16in. x 107ft 5in. x 55ft 7in. (5.638m x 32.741m x 16.942m)
Materials:
Titanium
Physical Description:
Twin-engine, two-seat, supersonic strategic reconnaissance aircraft; airframe constructed largley of titanium and its alloys; vertical tail fins are constructed of a composite (laminated plastic-type material) to reduce radar cross-section; Pratt and Whitney J58 (JT11D-20B) turbojet engines feature large inlet shock cones.
Long Description:
No reconnaissance aircraft in history has operated in more hostile airspace or with such complete impunity than the SR-71 Blackbird. It is the fastest aircraft propelled by air-breathing engines. The Blackbird’s performance and operational achievements placed it at the pinnacle of aviation technology developments during the Cold War. The airplane was conceived when tensions with communist Eastern Europe reached levels approaching a full-blown crisis in the mid-1950s. U.S. military commanders desperately needed accurate assessments of Soviet worldwide military deployments, particularly near the Iron Curtain. Lockheed Aircraft Corporation’s subsonic U-2 (see NASM collection) reconnaissance aircraft was an able platform but the U. S. Air Force recognized that this relatively slow aircraft was already vulnerable to Soviet interceptors. They also understood that the rapid development of surface-to-air missile systems could put U-2 pilots at grave risk. The danger proved reality when a U-2 was shot down by a surface to air missile over the Soviet Union in 1960.
Lockheed’s first proposal for a new high speed, high altitude, reconnaissance aircraft, to be capable of avoiding interceptors and missiles, centered on a design propelled by liquid hydrogen. This proved to be impracticable because of considerable fuel consumption. Lockheed then reconfigured the design for conventional fuels. This was feasible and the Central Intelligence Agency (CIA), already flying the Lockheed U-2, issued a production contract for an aircraft designated the A-12. Lockheed’s clandestine ‘Skunk Works’ division (headed by the gifted design engineer Clarence L. "Kelly" Johnson) designed the A-12 to cruise at Mach 3.2 and fly well above 18,288 m (60,000 feet). To meet these challenging requirements, Lockheed engineers overcame many daunting technical challenges. Flying more than three times the speed of sound generates 316° C (600° F) temperatures on external aircraft surfaces, which are enough to melt conventional aluminum airframes. The design team chose to make the jet’s external skin of titanium alloy to which shielded the internal aluminum airframe. Two conventional, but very powerful, afterburning turbine engines propelled this remarkable aircraft. These power plants had to operate across a huge speed envelope in flight, from a takeoff speed of 334 kph (207 mph) to more than 3,540 kph (2,200 mph). To prevent supersonic shock waves from moving inside the engine intake causing flameouts, Johnson’s team had to design a complex air intake and bypass system for the engines.
Skunk Works engineers also optimized the A-12 cross-section design to exhibit a low radar profile. Lockheed hoped to achieve this by carefully shaping the airframe to reflect as little transmitted radar energy (radio waves) as possible, and by application of special paint designed to absorb, rather than reflect, those waves. This treatment became one of the first applications of stealth technology, but it never completely met the design goals.
Test pilot Lou Schalk flew the single-seat A-12 on April 24, 1962, after he became airborne accidentally during high-speed taxi trials. The airplane showed great promise but it needed considerable technical refinement before the CIA could fly the first operational sortie on May 31, 1967 – a surveillance flight over North Vietnam. A-12s, flown by CIA pilots, operated as part of the Air Force’s 1129th Special Activities Squadron under the "Oxcart" program. While Lockheed continued to refine the A-12, the U. S. Air Force ordered an interceptor version of the aircraft designated the YF-12A. The Skunk Works, however, proposed a "specific mission" version configured to conduct post-nuclear strike reconnaissance. This system evolved into the USAF’s familiar SR-71.
Lockheed built fifteen A-12s, including a special two-seat trainer version. Two A-12s were modified to carry a special reconnaissance drone, designated D-21. The modified A-12s were redesignated M-21s. These were designed to take off with the D-21 drone, powered by a Marquart ramjet engine mounted on a pylon between the rudders. The M-21 then hauled the drone aloft and launched it at speeds high enough to ignite the drone’s ramjet motor. Lockheed also built three YF-12As but this type never went into production. Two of the YF-12As crashed during testing. Only one survives and is on display at the USAF Museum in Dayton, Ohio. The aft section of one of the "written off" YF-12As which was later used along with an SR-71A static test airframe to manufacture the sole SR-71C trainer. One SR-71 was lent to NASA and designated YF-12C. Including the SR-71C and two SR-71B pilot trainers, Lockheed constructed thirty-two Blackbirds. The first SR-71 flew on December 22, 1964. Because of extreme operational costs, military strategists decided that the more capable USAF SR-71s should replace the CIA’s A-12s. These were retired in 1968 after only one year of operational missions, mostly over southeast Asia. The Air Force’s 1st Strategic Reconnaissance Squadron (part of the 9th Strategic Reconnaissance Wing) took over the missions, flying the SR-71 beginning in the spring of 1968.
After the Air Force began to operate the SR-71, it acquired the official name Blackbird– for the special black paint that covered the airplane. This paint was formulated to absorb radar signals, to radiate some of the tremendous airframe heat generated by air friction, and to camouflage the aircraft against the dark sky at high altitudes.
Experience gained from the A-12 program convinced the Air Force that flying the SR-71 safely required two crew members, a pilot and a Reconnaissance Systems Officer (RSO). The RSO operated with the wide array of monitoring and defensive systems installed on the airplane. This equipment included a sophisticated Electronic Counter Measures (ECM) system that could jam most acquisition and targeting radar. In addition to an array of advanced, high-resolution cameras, the aircraft could also carry equipment designed to record the strength, frequency, and wavelength of signals emitted by communications and sensor devices such as radar. The SR-71 was designed to fly deep into hostile territory, avoiding interception with its tremendous speed and high altitude. It could operate safely at a maximum speed of Mach 3.3 at an altitude more than sixteen miles, or 25,908 m (85,000 ft), above the earth. The crew had to wear pressure suits similar to those worn by astronauts. These suits were required to protect the crew in the event of sudden cabin pressure loss while at operating altitudes.
To climb and cruise at supersonic speeds, the Blackbird’s Pratt & Whitney J-58 engines were designed to operate continuously in afterburner. While this would appear to dictate high fuel flows, the Blackbird actually achieved its best "gas mileage," in terms of air nautical miles per pound of fuel burned, during the Mach 3+ cruise. A typical Blackbird reconnaissance flight might require several aerial refueling operations from an airborne tanker. Each time the SR-71 refueled, the crew had to descend to the tanker’s altitude, usually about 6,000 m to 9,000 m (20,000 to 30,000 ft), and slow the airplane to subsonic speeds. As velocity decreased, so did frictional heat. This cooling effect caused the aircraft’s skin panels to shrink considerably, and those covering the fuel tanks contracted so much that fuel leaked, forming a distinctive vapor trail as the tanker topped off the Blackbird. As soon as the tanks were filled, the jet’s crew disconnected from the tanker, relit the afterburners, and again climbed to high altitude.
Air Force pilots flew the SR-71 from Kadena AB, Japan, throughout its operational career but other bases hosted Blackbird operations, too. The 9th SRW occasionally deployed from Beale AFB, California, to other locations to carryout operational missions. Cuban missions were flown directly from Beale. The SR-71 did not begin to operate in Europe until 1974, and then only temporarily. In 1982, when the U.S. Air Force based two aircraft at Royal Air Force Base Mildenhall to fly monitoring mission in Eastern Europe.
When the SR-71 became operational, orbiting reconnaissance satellites had already replaced manned aircraft to gather intelligence from sites deep within Soviet territory. Satellites could not cover every geopolitical hotspot so the Blackbird remained a vital tool for global intelligence gathering. On many occasions, pilots and RSOs flying the SR-71 provided information that proved vital in formulating successful U. S. foreign policy. Blackbird crews provided important intelligence about the 1973 Yom Kippur War, the Israeli invasion of Lebanon and its aftermath, and pre- and post-strike imagery of the 1986 raid conducted by American air forces on Libya. In 1987, Kadena-based SR-71 crews flew a number of missions over the Persian Gulf, revealing Iranian Silkworm missile batteries that threatened commercial shipping and American escort vessels.
As the performance of space-based surveillance systems grew, along with the effectiveness of ground-based air defense networks, the Air Force started to lose enthusiasm for the expensive program and the 9th SRW ceased SR-71 operations in January 1990. Despite protests by military leaders, Congress revived the program in 1995. Continued wrangling over operating budgets, however, soon led to final termination. The National Aeronautics and Space Administration retained two SR-71As and the one SR-71B for high-speed research projects and flew these airplanes until 1999.
On March 6, 1990, the service career of one Lockheed SR-71A Blackbird ended with a record-setting flight. This special airplane bore Air Force serial number 64-17972. Lt. Col. Ed Yeilding and his RSO, Lieutenant Colonel Joseph Vida, flew this aircraft from Los Angeles to Washington D.C. in 1 hour, 4 minutes, and 20 seconds, averaging a speed of 3,418 kph (2,124 mph). At the conclusion of the flight, ‘972 landed at Dulles International Airport and taxied into the custody of the Smithsonian’s National Air and Space Museum. At that time, Lt. Col. Vida had logged 1,392.7 hours of flight time in Blackbirds, more than that of any other crewman.
This particular SR-71 was also flown by Tom Alison, a former National Air and Space Museum’s Chief of Collections Management. Flying with Detachment 1 at Kadena Air Force Base, Okinawa, Alison logged more than a dozen ‘972 operational sorties. The aircraft spent twenty-four years in active Air Force service and accrued a total of 2,801.1 hours of flight time.
Wingspan: 55’7"
Length: 107’5"
Height: 18’6"
Weight: 170,000 Lbs
Reference and Further Reading:
Crickmore, Paul F. Lockheed SR-71: The Secret Missions Exposed. Oxford: Osprey Publishing, 1996.
Francillon, Rene J. Lockheed Aircraft Since 1913. Annapolis, Md.: Naval Institute Press, 1987.
Johnson, Clarence L. Kelly: More Than My Share of It All. Washington D.C.: Smithsonian Institution Press, 1985.
Miller, Jay. Lockheed Martin’s Skunk Works. Leicester, U.K.: Midland Counties Publishing Ltd., 1995.
Lockheed SR-71 Blackbird curatorial file, Aeronautics Division, National Air and Space Museum.
DAD, 11-11-01