Most CNC turning machines in precision machining factory are furnished with canned cycles equipped for performing unpleasant turning/exhausting and complete the process of; turning/exhausting. The G71 canned cycle takes various roughing passes on the workpiece while keeping a steady profundity of cut. Harsh/complete the process of turning is written in a fraction of the squares of code that it would take to compose without the canned cycle.
OD Turning Canned Cycle
Before starting the canned cycle for an external distance across turning operation the apparatus is situated at a beginning point. Toward the finish of the canned cycle the instrument will re-visitation of this equivalent point. This position is usually near the corner of where the face and the stock OD meet with clearance in both the X-and Z-tomahawks. This initial placing shows to the machine where the beginning stock measurement is and where the canned cycle will start eliminating material. The device of precision cnc machining china will naturally re-visitation of this moment that the cycle is finished. The roughing passes will begin at the external measurement and work internal until the harsh mold is finished.
Each pass will start by gradually venturing internal in the X-pivot bearing and afterward cut straight in the Z-negative course. After the heft of the material has been taken out, the cycle will make a last harsh shaping pass while leaving a completion allowance. This last pass smooths out any means gave up from different passes.
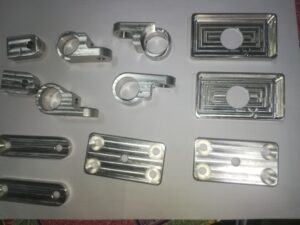
Numerous Fanuc controls require two sequential G71 blocks for the roughing cycle while Has require just one. These squares regularly use factors, for example, u, R, P, Q, w, and F. For a Fanuc, a portion of similar characters utilized for factors on the main square are rehashed on the second with a different meaning, so be cautious when programming.
The primary G71 block for a Fanuc may utilize the accompanying:
. U sets the profundity of cut for each roughing pass (spiral worth).
. R sets the distance the device will withdraw from each roughing pass prior to taking a fast action to the start of the following pass.
The second G71 block for a Fanuc may utilize the accompanying:
. P indicates the grouping number where the code for the form starts.
. Q determines the grouping number where the code for the form closes.
. U sets the measure of material to be left on all distances across for later finishing.
. w sets the measure of material to be left on all countenances for later wrapping up.
. F sets the roughing feed rate. The essential Has G71 block contains the following:
. P specifies the arrangement number where the code for the shape starts.
. Q specifies the grouping number where the code for the shape closes.
. D sets the profundity of cut for each roughing pass.
.U sets the measure of material to be left on all breadths for later wrapping up.
. W sets the measure of material to be left on all appearances for later finishing.
. F sets the roughing feed rate.
The table underneath shows the configurations utilized on numerous Fanuc and Haas machines. This article is from http://www.tinymachining.com/