Roughing and Finishing
In machine tasks, and all machining, there is harsh cutting and complete the process of cutting. The reason for unpleasant cutting, or roughing, is to eliminate however much material as fast as could be expected to draw near to the ideal size. There is little worry for making a smooth surface. Roughing utilizes more slow cutting velocities, more profound cuts, and higher feed rates.
Subsequent to roughing, complete the process of cutting, or completing, is utilized to deliver a smoother surface and carry the part to the last wanted size. Completing utilizations higher cutting rates, lighter cuts, and lower feed rates. cnc precision machining companies sums up roughing and completing and the connection among roughing and completing and profundity of Cut, speed, and feed.
Machining Time Calculation
It might be imperative to appraise the time needed to play out a machine activity or tasks. This is indispensable while machining huge parts or enormous quantities of parts. Machining time can be determined by china 4 axis cnc machining utilizing the accompanying equation. The accompanying models are outrageous and may not be normal, yet they show the significance of having the option to figure assessed machining time.
GENERAL LATHE SAFETY
Like any machine instrument, the machine can be extremely risky, however by watching a couple of fundamental precautionary measures, safe activity can be guaranteed. Explicit wellbeing notes are appeared all through this unit, yet following are a few insurances that ought to be seen during cnc lathe machining all kinds of precision metal parts factory.
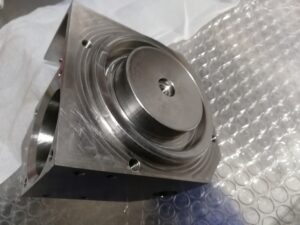
- Always wear ANSI Z87 appraised security glasses while working a machine.
- Wear suitable hard-soled work shoes.
- Wear short sleeves or move up long sleeves past the elbows.
- Do not wear any free attire that can become trapped in moving machine parts.
- Remove watches, rings, and other adornments.
- Secure long hair so it can’t get tangled in moving machine parts.
- Make sure all machine monitors and covers are set up before working any machine.
- Avoid expanding long workpieces past the left finish of the headstock.
- Never work a machine that is bolted out or labeled out or eliminate someone else’s lock or tag.
- When working a machine, remain zeroed in on the machine. Try not to get diverted by different exercises or converse with others.
- Never leave the machine while it is running.
- Do not let others change work, device, or machine settings and don’t change others’ arrangements.
- Avoid quickly and strongly moving cutting instruments into the workpiece. This can break devices and toss sharp parts toward the administrator. Little distance across and short workpieces can likewise be pulled from the pivoting workholding gadget.
- Never contact a workpiece or workholding gadget that is turning or endeavor to stop a machine axle by hand or with a cloth. Permit the axle to stop all alone.
- Always shut off the axle and let it reach a stand-still before changing workholding or toolholding gadgets, to take estimations, or to clean the machine.
- Remove chips from the workpiece and device utilizing a brush, forceps, or a chip snare simply after the shaft has reached a stand-still. Never eliminate chips by hand.
- Never utilize packed air to clean chips, garbage, and cutting liquids from the machine.
- This article is from http://www.tinymachining.com